In-Mold Decorations: Elevating Products With Accuracy and Appearances
In the world of product layout, the marriage of precision and appearance holds a vital setting in recording customer attention and commitment. In-Mold Decorations (IMD) have arised as a sophisticated strategy that not only boosts the visual appeal of products yet likewise ensures a careful integration of layout elements.
Advantages of In-Mold Decorations
Making use of in-mold designs offers producers an economical technique to perfectly incorporate elaborate styles onto plastic surfaces during the manufacturing process. This ingenious strategy involves putting a pre-printed movie or label right into the mold and mildew before infusing the molten plastic, causing a permanent combination of the decor with the product. The advantages of in-mold decors are manifold, starting with the capability to accomplish high-resolution graphics and detailed designs that boost the visual appeal of the last item. This procedure removes the need for secondary operations such as painting or post-decoration, enhancing the production procedure and lowering manufacturing time and costs.
In enhancement to enhancing visual appeals, in-mold designs likewise enhance the sturdiness and durability of the style as it ends up being an important part of the product, as opposed to a surface layer that can subside over time. Additionally, the smooth combination of designs through in-mold techniques ensures a uniform and consistent look throughout all produced items, maintaining brand name consistency and quality criteria. Generally, the benefits of in-mold decors make it a favored selection for makers wanting to boost their products with accuracy and aesthetic appeal
Precision in Layout Combination
Achieving thorough design assimilation through in-mold decors needs an eager concentrate on accuracy and attention to information from the initial stages of the production process. The success of in-mold decors hinges on the smooth assimilation of the style with the item, creating a aesthetically appealing and unified end outcome. Precision in style assimilation involves aspects such as guaranteeing the precise positioning of the decoration within the mold and mildew, selecting the best products to attain the desired visual, and keeping consistency throughout the manufacturing procedure.
One secret element of precision in design integration is the alignment of the decoration with the item's attributes and shapes. Furthermore, interest to detail is essential in maintaining the quality and uniformity of the decors across multiple production runs, ensuring that each item satisfies the greatest standards of accuracy and visual charm.
Appearances and Aesthetic Effect
With a focus on boosting the general charm of products, the appearances and aesthetic impact of in-mold decorations play a crucial function in captivating customer interest. In today's open market, where customers are swamped with choices, the aesthetic charm of a product can be the distinguishing aspect that affects getting decisions. In-mold decors use a distinct possibility to raise the visual appeals of items by offering detailed styles, vibrant shades, and seamless surfaces that traditional designing methods might struggle to accomplish.
The visual effect of in-mold decorations prolongs past mere appearances; it interacts brand name identity, high quality, and attention to information. By incorporating visually enticing check out here components into product layout, manufacturers can create a solid brand name visibility that resonates with consumers on a subconscious degree. In addition, the accuracy and consistency provided by in-mold design strategies ensure that every product meets the greatest criteria of aesthetic allure, reinforcing brand trustworthiness and consumer trust fund.
Cost-Effectiveness of IMD
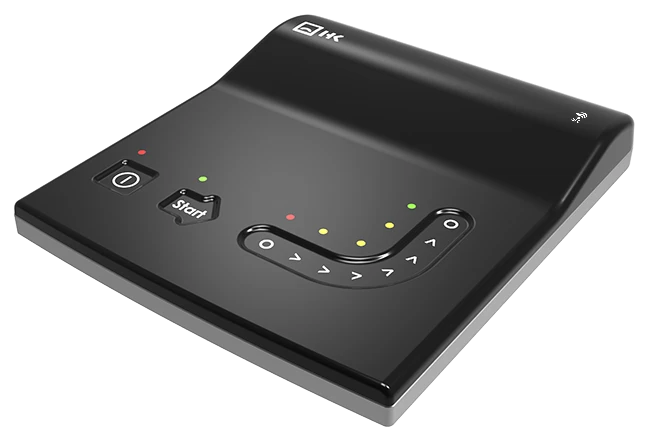
IMD minimizes the requirement for second procedures like paint or labeling, conserving both time and resources. By integrating the design directly into the molding process, IMD eliminates the additional actions needed for using designs post-production. This structured process not only decreases labor costs however additionally minimizes the threat of mistakes or flaws that might occur during secondary decorating procedures.
In addition, IMD boosts the durability of decors by enveloping them within the item, making sure a longer-lasting and much more resistant finish - In-Mold Decorations. This longevity converts into decreased upkeep and substitute expenses over the product's lifecycle, making IMD a cost-effective remedy for accomplishing exceptional visual appeals and visual allure in manufacturing
Longevity and Durability
Incorporating in-mold decors not only makes certain cost-effectiveness in producing procedures however additionally substantially enhances item resilience and long life. The process of in-mold decor involves the application of graphics or ornamental finishes during the molding procedure, creating a integrated and smooth design that is shielded within the product itself. This protective layer given by in-mold decorations acts as a shield versus deterioration, scrapes, fading, and various other ecological variables that could jeopardize the look and sturdiness of the product with time.
Products with in-mold decorations are understood for their resistance to abrasion, chemicals, and UV direct exposure, making them perfect for applications that call for long-term performance and looks. Unlike traditional surface-applied designs that can peel or discolor with use, in-mold decorations end up being an inherent component of the item, guaranteeing that the style continues to be vivid and intact throughout the item's life-span. This durability not only enhances the overall quality of the product however explanation likewise minimizes the demand for constant upkeep or substitutes, ultimately providing long-term cost savings for consumers and producers alike.
Final Thought

The advantages of in-mold designs are manifold, starting with the ability to achieve high-resolution graphics and comprehensive designs that enhance the aesthetic allure of the last item.In addition to enhancing aesthetic appeals, in-mold designs also enhance the durability and longevity of the layout as it ends up being an integral component of the product, you could look here rather than a superficial layer that can put on off over time. In-mold decors use a special chance to elevate the visual appeals of products by giving complex styles, vibrant shades, and seamless finishes that typical designing methods might have a hard time to achieve.
The procedure of in-mold design involves the application of graphics or attractive surfaces during the molding procedure, producing a integrated and smooth style that is protected within the item itself. Unlike typical surface-applied decors that can peel off or discolor with use, in-mold decors become an inherent part of the item, guaranteeing that the design stays intact and brilliant throughout the product's life-span.
Comments on “Enhancing Product Appearances: The Duty of In-Mold Decorations in Production”